MIXERS MADE OF PLASTIC AND METAL
INDUSTRIAL MIXER SELECTION GUIDE
HOW TO CORRECTLY SIZE A MIXER FOR INDUSTRIAL LIQUIDS AND CORROSIVE SOLUTIONS
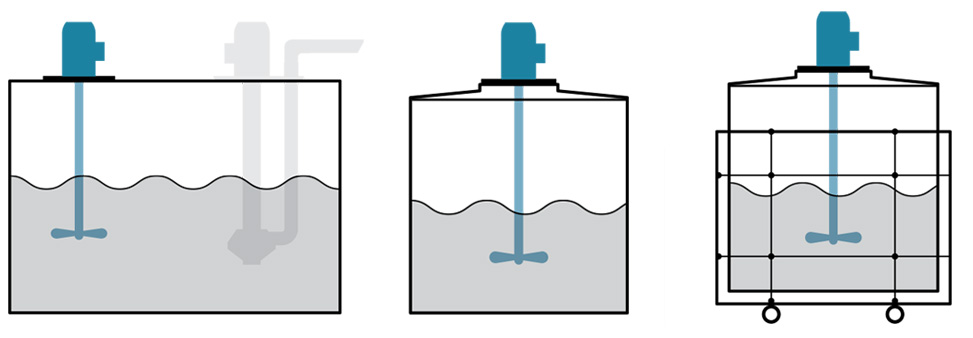
it can dissolve soluble solids, it can make heat exchange efficient, it can maintain particular temperatures. However, correct mixing and blending are always the result of a combination of several elements, including: general principles of hydraulics, physical characteristics of the container, duration of the operations to be carried out and the chemical nature of the fluids treated. The effectiveness of the mixing process is strongly influenced by these variables and their mutual interaction. The first step to obtaining satisfactory results is to describe your requirements to the manufacturer of the mixer, who will recommend the most appropriate model for your particular case.
FOUR STEPS TO CONFIGURING A MIXER
The information which is crucial to the sizing of a mixer is often quite hard to focus on. Sometimes it is so vague as to be unclear even to the user. As a rough guide, however, there are four steps to identifying the best stirrer and, consequently, to achieving an efficient mixing process.
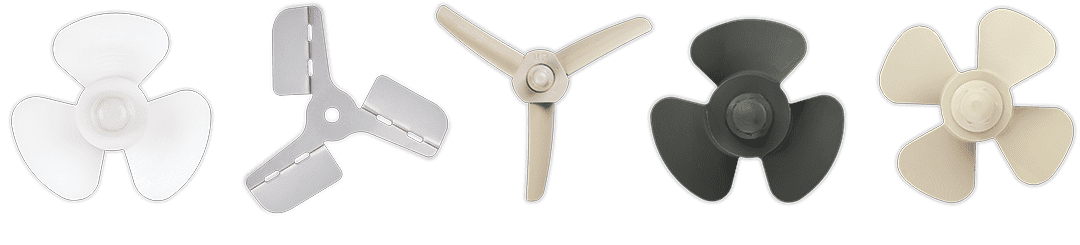
1 – PRELIMINARY INFORMATION
The configuration of a mixer for industrial applications requires the preliminary collection and assessment of some fundamental information. This is the starting point for choosing the size suited to the specific application and the construction material (plastic or metal) compatible with the aggressive nature of the liquids to be mixed. These are choices which, given the complexity of the machinery, are always best left to those who have been used to making this selection for years, like our company! It is particularly necessary to communicate exactly:
- the purpose of the process (mixing, solids suspension, heat maintenance, etc.)
- the total volume (of liquids and/or solids) to be handled
- the depth of the tank (or the length of the mixer)
- the level of the liquid: constant or variable (if variable: indication of minimum and maximum levels)
- the possible presence of baffles or flow breakers
- the rotation speed required by the process (strong, moderate, mild)
- the need to fit gearmotors or inverters (to manage the rotation speed).
- the chemical nature, density, viscosity and temperature of the liquid to be mixed
- the way in which the mixer is anchored to the tank (support flange)
- undesirable phenomena (formation of foam, air entrapment, permanence of surface dusts, etc.)
2 – MIXER POSITIONING
The position of the mixer inside the container is an important aspect which should not be underestimated. As you can easily imagine, the best point of installation for each stirrer depends on the shape and size of the container (cylindrical, rectangular, cubic), the height of the propeller in relation to the bottom of the tank and the shape of the lower part of the tank (flat, round or conical). Sometimes, in small containers, to overcome the inconveniences caused by the tangential flow, as an alternative to the baffles, the mixer is off-centre or angle mounted: however, these solutions only partially prevent the liquid from swirling around and easily cause high hydraulic loads with possible vibrations or unbalanced operation of the shaft.
G: mixer length
L: tank depth
L1: maximum level
L2: minimum level
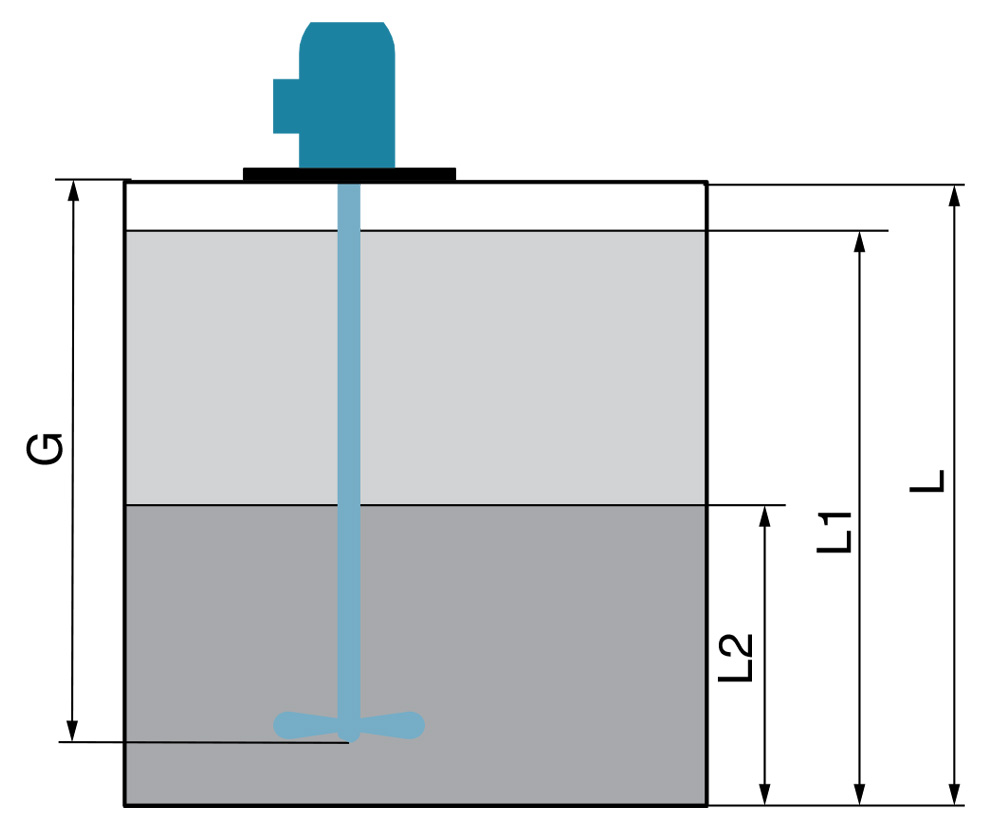
G: mixer length
L: tank depth
L1: maximum level
L2: minimum level
3 – CONTAINER GEOMETRY
The geometry of the container must be well defined in terms of shape and dimensions If the mixer works in a vertical cylindrical tank, the latter must have suitable vertical plates (baffles) to prevent rotation of the entire liquid mass and the formation of strong central vortices. If the mixer is installed in a conical basin, it is also important to know the dimensions of the conical part (in this case, too, the use of a proper baffling is recommended). The most efficient tanks are usually those with equal height, width and length dimensions and those with a convex or conical bottom: the movement will be more even and the emptying and cleaning operations will be easier.
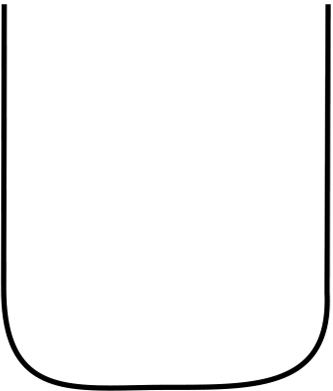
Tank with round bottom
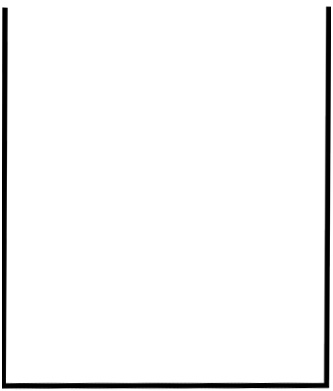
Tank with flat bottom
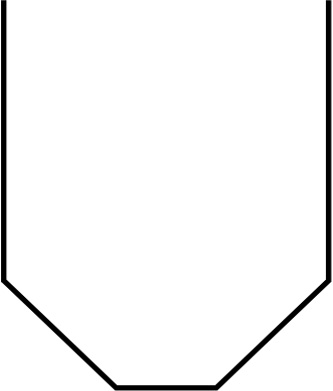
Tank with conical bottom
4 – FLOW PATTERNS
The flow from the mixer blades consists of three components: axial (downwards or upwards), radial (towards the container walls), tangential (rotary motion). Due to the rotation of the impeller, the mass of liquid rotates around the axis of the mixer: this could cause the formation of vortices or a decrease in relative speeds within the volume of liquid being mixed. This must be taken into consideration. It is also advisable to specify undesirable phenomena, such as the formation of foam, air entrapment, permanence of surface dusts, etc. Correct mixing must ensure a mixed flow that includes all three components. Savino Barbera mixers can also be fitted with symmetrical marine propellers: reversing their direction of rotation automatically reverses the mixing direction.
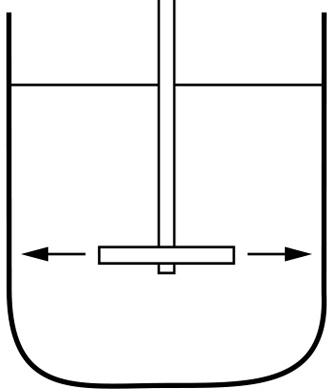
Radial mixing
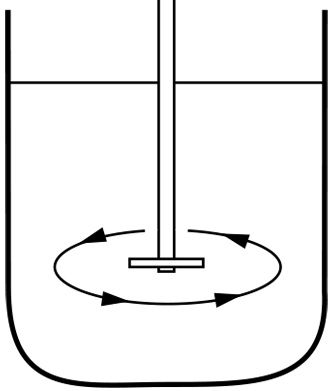
Tangential mixing
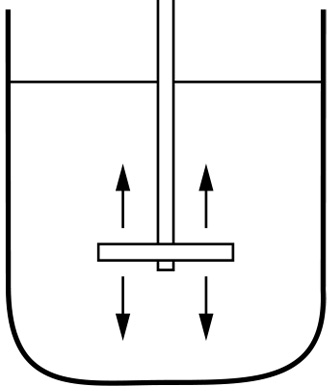
Axial mixing
download area
CHEMICALLY-RESISTANT PUMPS AND MIXERS
DO YOU HAVE A REQUEST ?
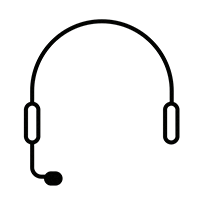
TALK TO OUR EXPERTS
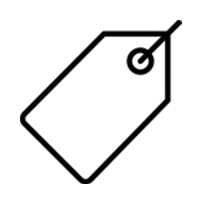